Report Coverage
This report on the clay and concrete bricks industry contains information on notable players and developments in the industry and factors that influence it, specifically the state of the construction industry. There are profiles of 21 companies including Corobrik, Brikor, Ocon, Ingonyama Blocks and Rheebok Brick Operations. \r\n
Introduction
• The brick manufacturing industry, which comprises clay and concrete bricks, is closely linked to the construction sector, which has been affected by the poor economy and delays in the implementation of many of government’s infrastructure projects.
• The construction sector’s contribution to GDP has declined for several years.
• Clay brick manufacturers fared a bit better than concrete manufacturers in the past year due to increased activity in the residential building sector.
• 2023 is expected to be a slower year for residential building due to rising inflation, interest rate hikes, and the knock-on effects of increased interest on property owners.
Strengths
• Clay brick production is a source of income, job creation and skills development in rural areas.
• Formal clay brick sector is well regulated in terms of legislation.
Weaknesses
• The clay brick manufacturing process is energy intensive and not environmentally friendly.
• Concrete brick manufacturers rely on the public sector for large projects.
• High barriers to entry for formal clay brick manufacturers.
Opportunities
• Projects focusing on sustainability.
• The development of affordable housing.
• The rollout of infrastructure development projects.
Threats
• Climate change, especially floods, wildfires, and drought.
• Economic uncertainty, and rising inflation.
• Fuel price volatility and reduced gross profit margins.
• High electricity costs and loadshedding.
Outlook
• Despite the delay in civil infrastructure development, declining construction industry revenue and higher construction material costs, construction activity is gradually recovering.
• The National Infrastructure Plan 2050 provides a long-term roadmap for infrastructure development. Corobrik has invested in a new manufacturing plant, placing it well to take part in this development.
• The construction industry is expected to stabilise at 3% per annum from 2023 to 2026.
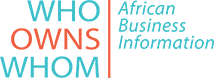
Full Report
R 6 500.00(ZAR) estimated $366.35 (USD)*
Industry Landscape
R 4 550.00(ZAR) estimated $ 256.44 (USD)*
Historical Reports
The Manufacture of Clay and Concrete Bricks Industry in South Africa 2019-01-17
R 1 900.00(ZAR) estimated $107.09 (USD)*
View Report Add to CartThe Manufacture of Clay and Concrete Bricks Industry in South Africa 2016-05-31
R 1 900.00(ZAR) estimated $107.09 (USD)*
View Report Add to CartThe Manufacture of Clay and Concrete Bricks Industry in South Africa 2014-08-18
R 1 900.00(ZAR) estimated $107.09 (USD)*
View Report Add to CartTable of Contents
[ Close ]PAGE | ||
---|---|---|
1. | INTRODUCTION | 5 |
2. | DESCRIPTION OF THE INDUSTRY | 5 |
2.1. | Industry Value Chain | 7 |
2.2. | Geographic Position | 8 |
2.3. | Size of the Industry | 9 |
3. | LOCAL | 9 |
3.1. | State of the Industry | 9 |
3.2. | Key Trends | 13 |
3.3. | Key Issues | 13 |
3.4. | Notable Players | 13 |
3.5. | Corporate Actions | 14 |
3.6. | Regulations | 15 |
3.7. | Enterprise Development and Social Development | 16 |
4. | AFRICA | 18 |
5. | INTERNATIONAL | 20 |
6. | INFLUENCING FACTORS | 21 |
6.1. | Loadshedding | 21 |
6.2. | Economic Environment | 21 |
6.3. | Input Costs | 22 |
6.4. | Labour | 23 |
6.5. | Environmental Issues | 24 |
6.6. | Technology, R&D, Innovation | 25 |
6.7. | Increasing Urbanisation and Need for Housing | 25 |
6.8. | Government Support | 26 |
7. | COMPETITIVE ENVIRONMENT | 26 |
7.1. | Competition | 26 |
7.2. | Ownership Structure of the Industry | 27 |
7.3. | Barriers to Entry | 28 |
8. | SWOT ANALYSIS | 28 |
9. | OUTLOOK | 29 |
10. | INDUSTRY ASSOCIATIONS | 29 |
11. | REFERENCES | 30 |
11.1. | Publications | 30 |
11.2. | Websites | 30 |
APPENDIX 1 | 31 | |
Summary of Notable Players | 31 | |
COMPANY PROFILES | 34 | |
Afrimat Ltd | 34 | |
Aveng Africa (Pty) Ltd | 40 | |
Brakkefontein Clay Products (Pty) Ltd | 45 | |
Brikor Ltd | 47 | |
Corobrik (Pty) Ltd | 51 | |
Deranco Blocks (Pty) Ltd | 54 | |
Good Hope Brick (Pty) Ltd | 56 | |
Grahamstown Brick (Pty) Ltd | 58 | |
Inca Concrete Products (Pty) Ltd | 60 | |
Infrastructure Specialist Group (Pty) Ltd | 62 | |
Ingonyama Blocks CC | 65 | |
J J Bricks (Pty) Ltd | 67 | |
L K Brick and Block Manufacturers (Pty) Ltd | 69 | |
Langkloof Steenwerwe (Pty) Ltd | 71 | |
Ngqura Brick (Pty) Ltd | 73 | |
Ocon Brick (Pty) Ltd | 75 | |
Rheebok Brick Operations (Pty) Ltd | 77 | |
S A Block (Pty) Ltd | 79 | |
West End Cement Bricks (Pty) Ltd | 81 | |
West End Claybrick (Pty) Ltd | 83 | |
Worcester Bakstene (Pty) Ltd | 85 |